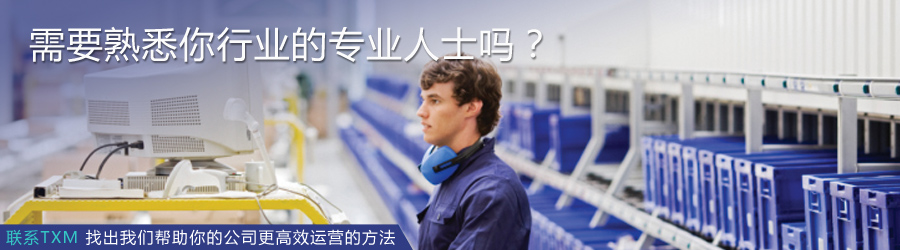
赛克斯赛艇 – 一个奥林匹克成功的故事
客户:杰夫赛克斯联合公司
地点:基隆,澳大利亚
早在2008年金融危机之前,全球领先的划艇制造商赛克斯赛艇就在基隆的一座小山上建立了多个小工厂。许多年前,赛克斯业务就已经从木材转移至先进的碳纤维复合材料,但制造的理念却没有改变。传统的“手艺”做法是一个人负责赛艇的生产全过程。在终检阶段,那些最熟练的工匠会仔细检查赛艇,几乎每艘赛艇都会有不同形式的返工。这种做法的结果是产出很不稳定并且积压的产品难以控制。在项目开始的时候,赛克斯有6个月的积压订单,并面临未来从中国进口赛艇的压力。
赛克斯的董事总经理杰夫•劳伦斯向基隆制造局的企业业务顾问做了一次免费的业务评估,结果显示需要引进精益生产理念。
TXM指导赛克斯团队开发了价值流图,在应用TXM的工厂布局流程后,赛克斯就真正上路了。结果是“S”型的布局可以使企业的潜在产出增加一倍,但需要从“一个人制造赛艇”转变成“单件流”并建立标准化作业。这个布局还考虑到了以每天一艘赛艇的速度依次在生产工序间移动。在层压和塑性工序间建立了小的先进先出通道,赛艇每天都需要移动以保持流动的顺畅。
为了平衡各工序之间的工作,赛克斯对每个流程步骤都做了标准化作业分析。这是个复杂的过程,因为每艘赛艇都是不一样的,标准化作业必须考虑到这一点。随后,赛克斯采用了TXM所说的“模糊化标准”作业,工作要素以几分钟为单位,必须允许工作之间的周期时间有所差异。同时,船上桨的装配件还增加了复杂性。在赛艇制造的同时,装配件也需经过完全不同的方法制作完成。装配件的延迟是造成赛艇积压的一个常见原因。赛克斯在金工车间改进了流程,以确保装配件可以在赛艇完工之前安装完成。
除了确保流动,标准化作业为生产力带来了明显的好处,完成任务的时间差异被突显了出来,所有作业员都遵循最佳的工作方法。经过初步的磨合,这种标准化作业的方法以及为赛克斯已有的高质量标准做了进一步的改善。
一旦标准化作业开始执行,最后阶段的重点将回到加强精益基础上来。5S、结构化的问题解决、以及精益日常管理,班组长通过每天简短的“站立”会议来指导他们的团队。这将确保赛克斯已经稳定了他们的流程,并持续改善。
结果已经蔚为壮观。除了有一个一尘不染的工厂,还拥有领先世界的生产率和质量。随着产量的增加,赛克斯已经将积压的订单从6个月减少至6周,生产率提升的同时还减少的返工。