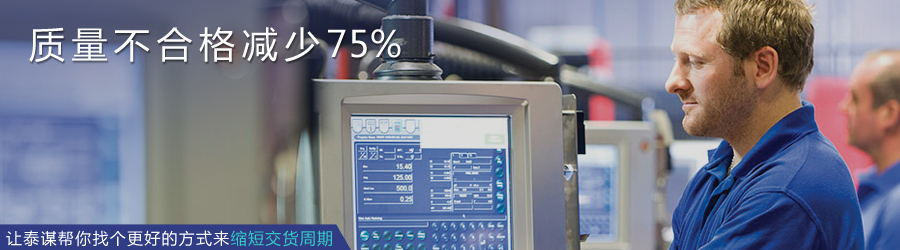
生产线重新设计和精益生产流程带来40%生产力的提升
客户:某全球高科技制造商
地点:墨尔本,澳大利亚
挑战
作为科学应用领域尖端设备的全球领导者,我们的客户正面临着重大的挑战。来自低成本国家的全球化增长和日益激烈的竞争,使得他们意识到需要在增加产出的同时降低其主要产品线的成本。虽然已经意识到实施精益生产20多年来的作用,但我们的客户不想要标准的‘精益101’做法,而是在寻找一个新的方法挑战自己,以使自己走在精益生产实践的前列。其目标是要驱逐浪费,减小生产面积和缩短交付周期。因此,他们找到了TXM。
TXM响应
TXM与生产团队一起对工厂进行了细致的评估 – 绘制了主产品线的价值流图,按照工厂布局最佳实践标准对其生产进行了评估,并导入5S审核以确定空间利用的有效性。然后,我们指导团队开发了一个新的工厂布局和生产理念,将连续流生产融入节拍时间,在各工序引入质量检验,开发高效的子装配单元,改善原物料的供应流程。另外延长了18个月的指导,以支持新生产线概念的实施,并确保团队掌握了这些知识。
结果
在TXM的帮助下,客户实现了业绩突破性的改善,包括40%的单位劳动成本改善 :
- 终检时间减少80%;
- 包装时间减少90%;
- 同时,子装配生产时间减少超过50%;
- 生产交付时间和在制品库存降低了75%。