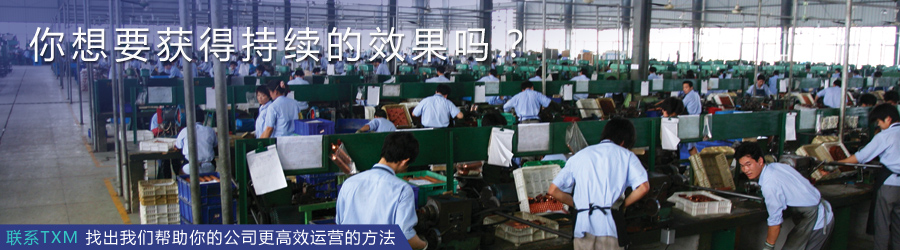
精益生产在医药行业改善OEE的应用
客户:全球领先的制药企业
地点:悉尼,澳大利亚
挑战
我们的客户是一家全球领先的制药企业。有一条关键的生产线为全球市场生产无菌液体药物。这条线预计有20%的销售增长。然而,专利期满意味着要大幅降低生产成本。为了降低成本,公司决定从四班七天生产变为三班五天生产。实现这一改进的同时,也要增加生产线60%的产出,以适应销售增长的需要。其中大约一半的改进来自设备投资,其他的得通过实施精益生产提高生产效率来实现。
TXM响应
TXM解决过许多制药公司实施精益生产时的共同问题。第一步首先要完成生产过程的价值流图。该图反映了自动灌装过程中,间歇高压釜和半自动包装过程之间的不平衡。这些不平衡导致了在制品的波动,以及灌装和包装过程的中断。TXM设立了一个简单的可视化系统来控制在制品数量,车间可以做标准化决策以保持整个价值流的平衡。
车间和领导行为的变化是实现变革的关键。每小时的产出都需要记录下来,如果小时产出目标没有达成,则需要通过问题解决来找到效率损失的根本原因。团队领导、经理和支持人员,包括维修和QA,都要学习如何给予有效及时的支持。这需要高层管理团队的文化变革,以确保所有部门都意识到支持车间创造价值的重要性。
换型时间的减少和标准化作业的的实施细化并巩固了取得的成果。
结果
该生产线在十个月的时间里达到了所要求的60%产能的增加,设备的改进贡献了四分之一,余下部分则来自工作实践的改善和文化的变革。OEE从约45%提高到75%。
更重要的是,这个项目成为了整个公司文化变革的催化剂,我们的客户可以运用学到的知识在其他生产线实现显著业绩的显著改善。
不到两个月的时间里,通过节约成本就已经收回了在TXM服务上的投入。